During the peak years of the British textile industry, textile mill owners made great efforts to reduce waste and recycle old clothes. This way of working is now being adopted more and more as modern manufacturers try to become more sustainable. For the Victorians, however, reducing waste and recycling clothes was about making as much money as possible.
Cotton
Waste was produced at almost every stage of the cotton spinning process. The light, fluffy fibres that make cotton great for making fabric can also lead to waste. When the cotton was being cleaned and combed in the carding engine, some of the fibres would fly off and settle on the floor, while others would get caught on the tiny wire pins that comb the cotton. This is where much of the waste was produced.
When the cotton was in the final stages of being spun—as it was stretched, twisted and wound onto bobbins—waste was created when the thin, taut threads snapped and the ends had to be twisted back together by a worker called a piecer. Small pieces of tightly twisted yarn fell to the floor underneath the machine where they were swept up by a scavenger, usually a child whose job it was to sweep up while avoiding being crushed by the heavy, fast-moving machinery. If you head to the Textiles Gallery at the Science and Industry Museum, see if you can spot any cotton waste caught on the machines or gathering under them.
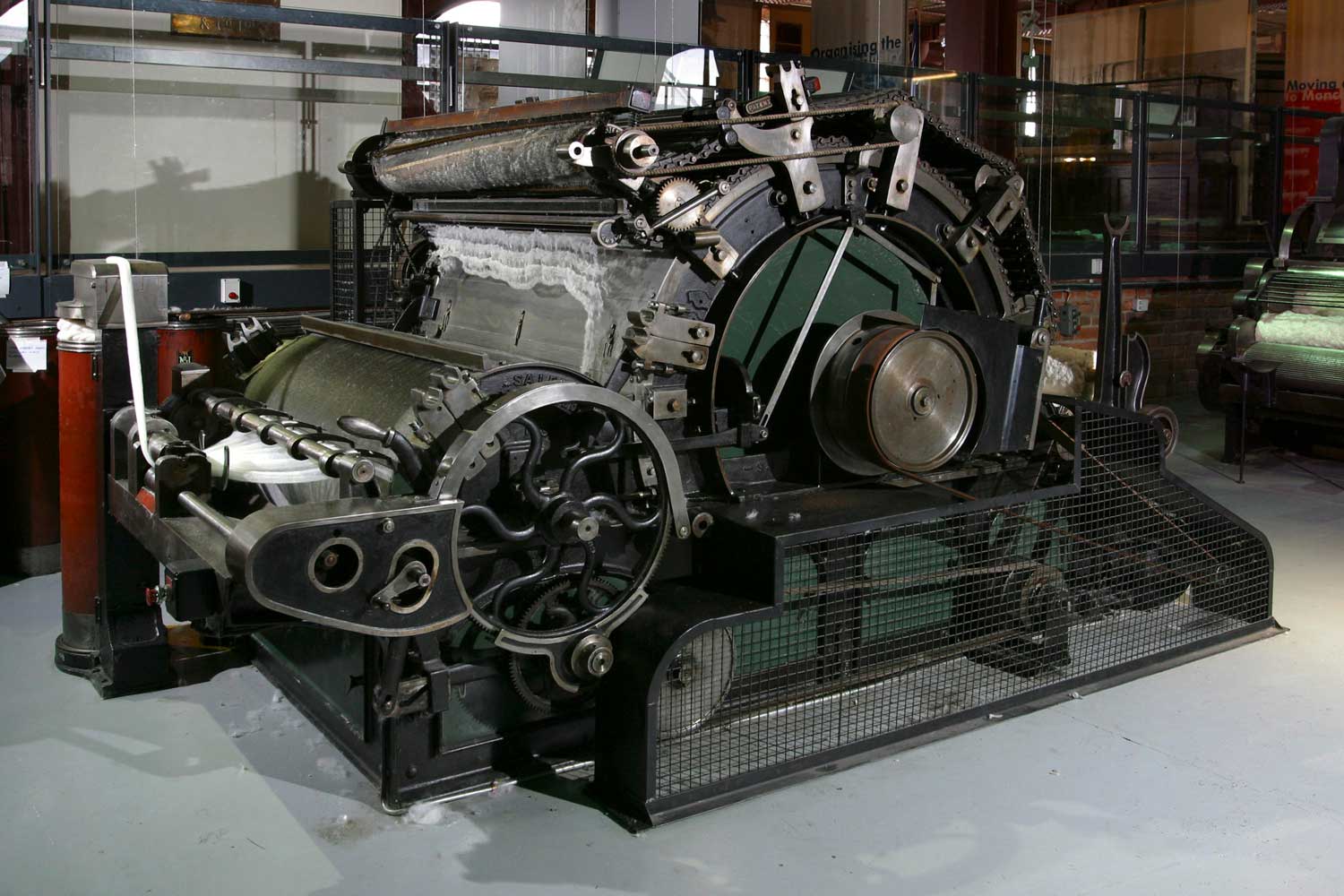
Credit: Science Museum Group Collection
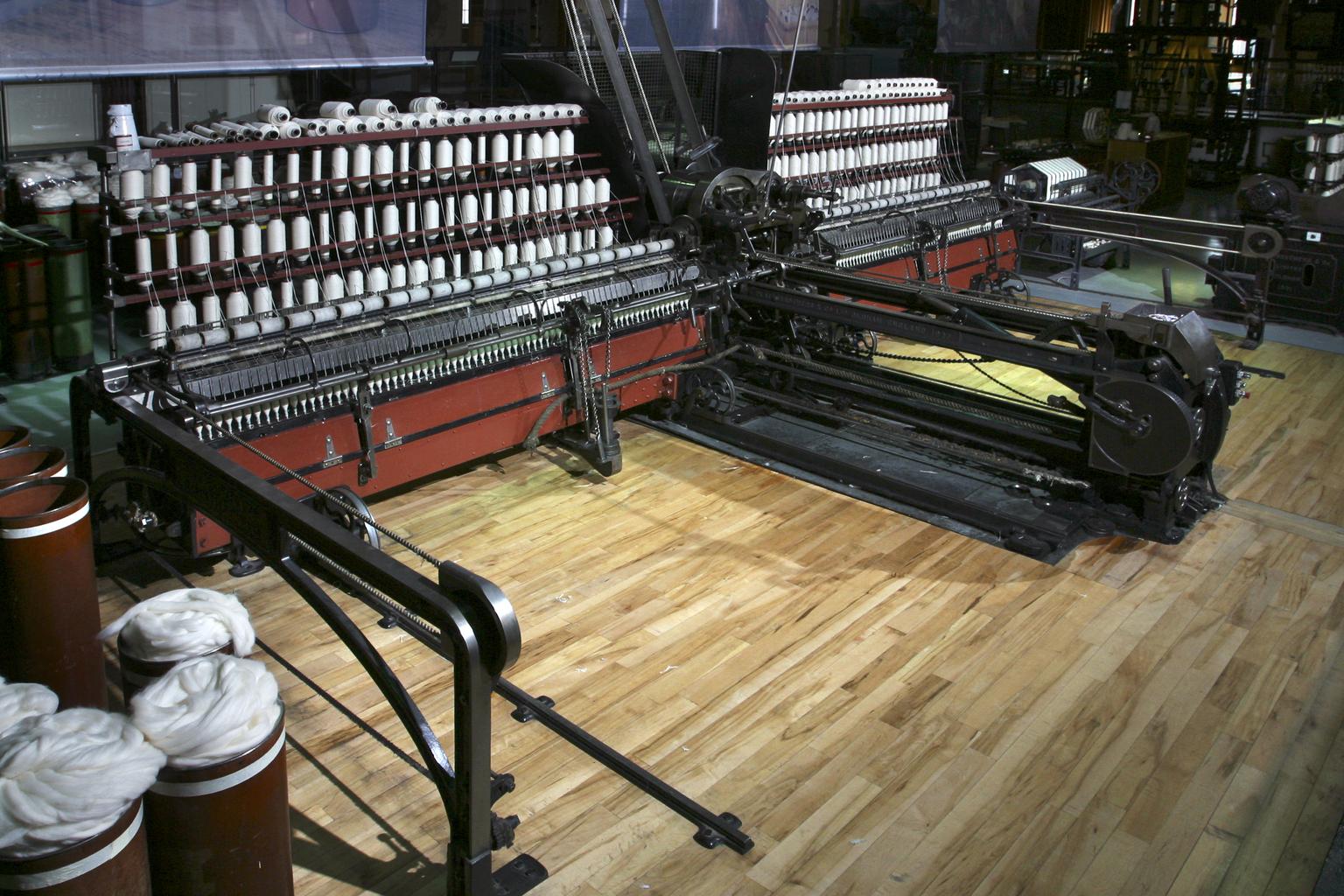
Photographed on display in the Textiles Gallery.
Credit: Science Museum Group Collection
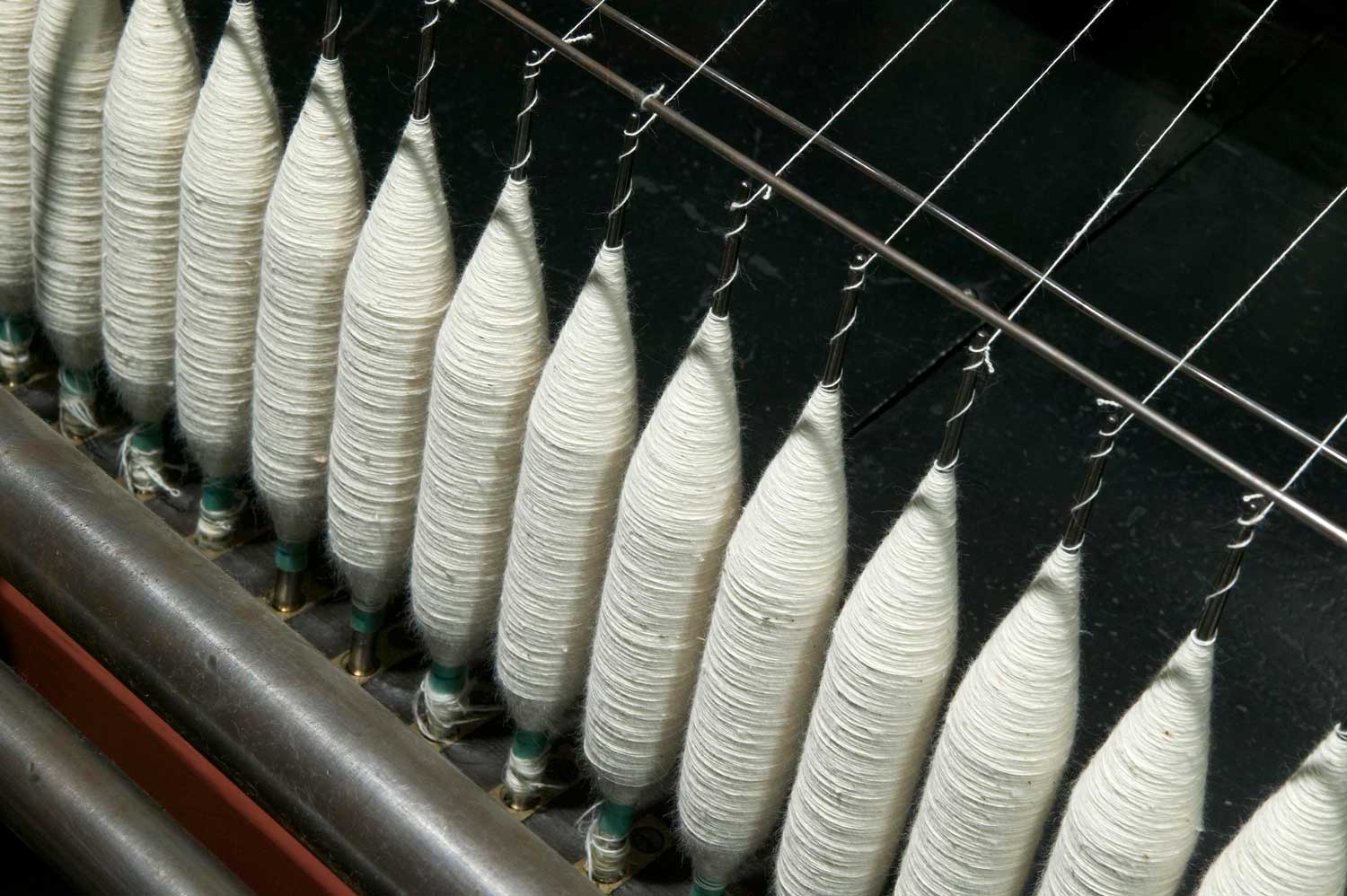
Credit: Science Museum Group Collection
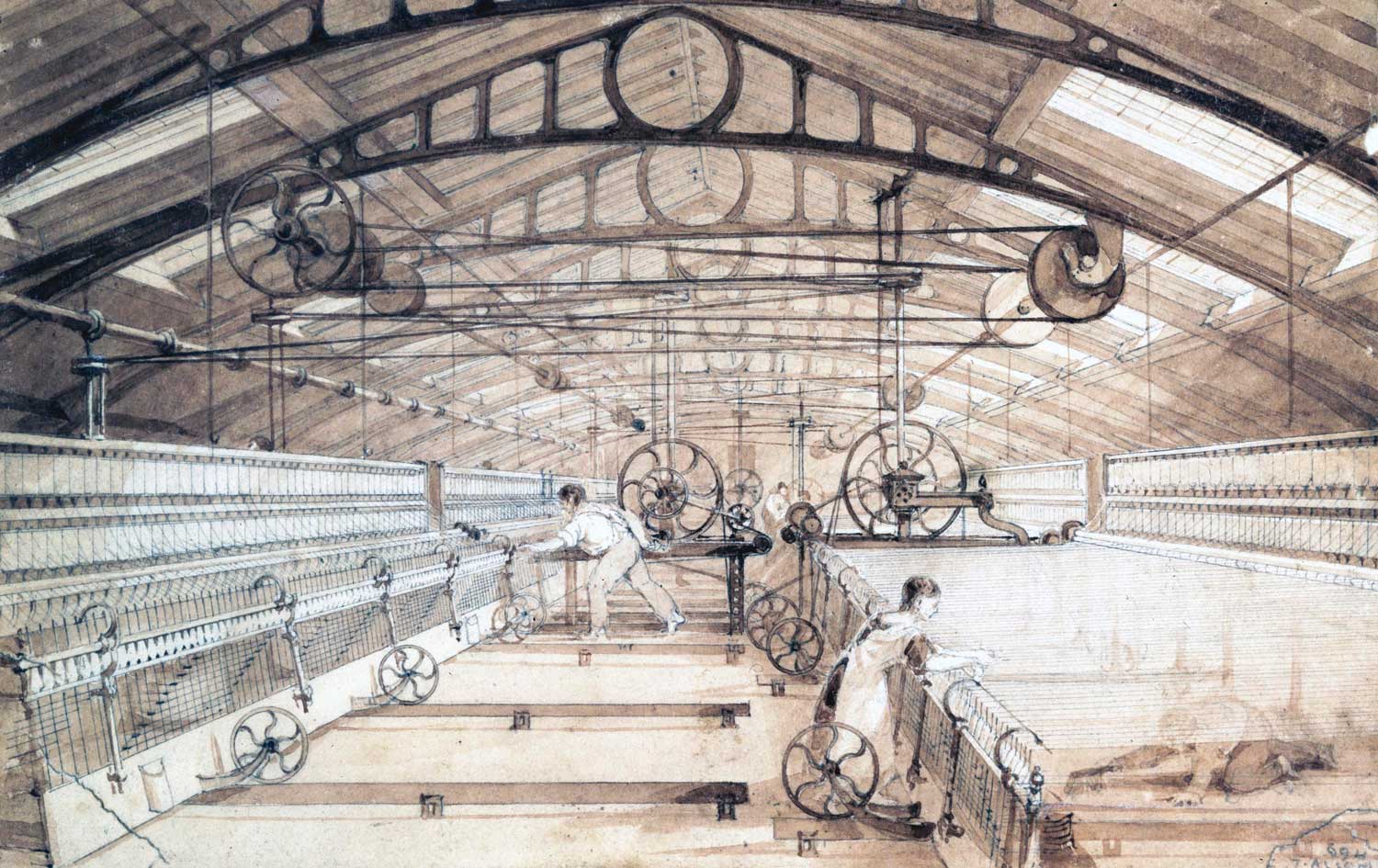
Credit: Science Museum Group Collection
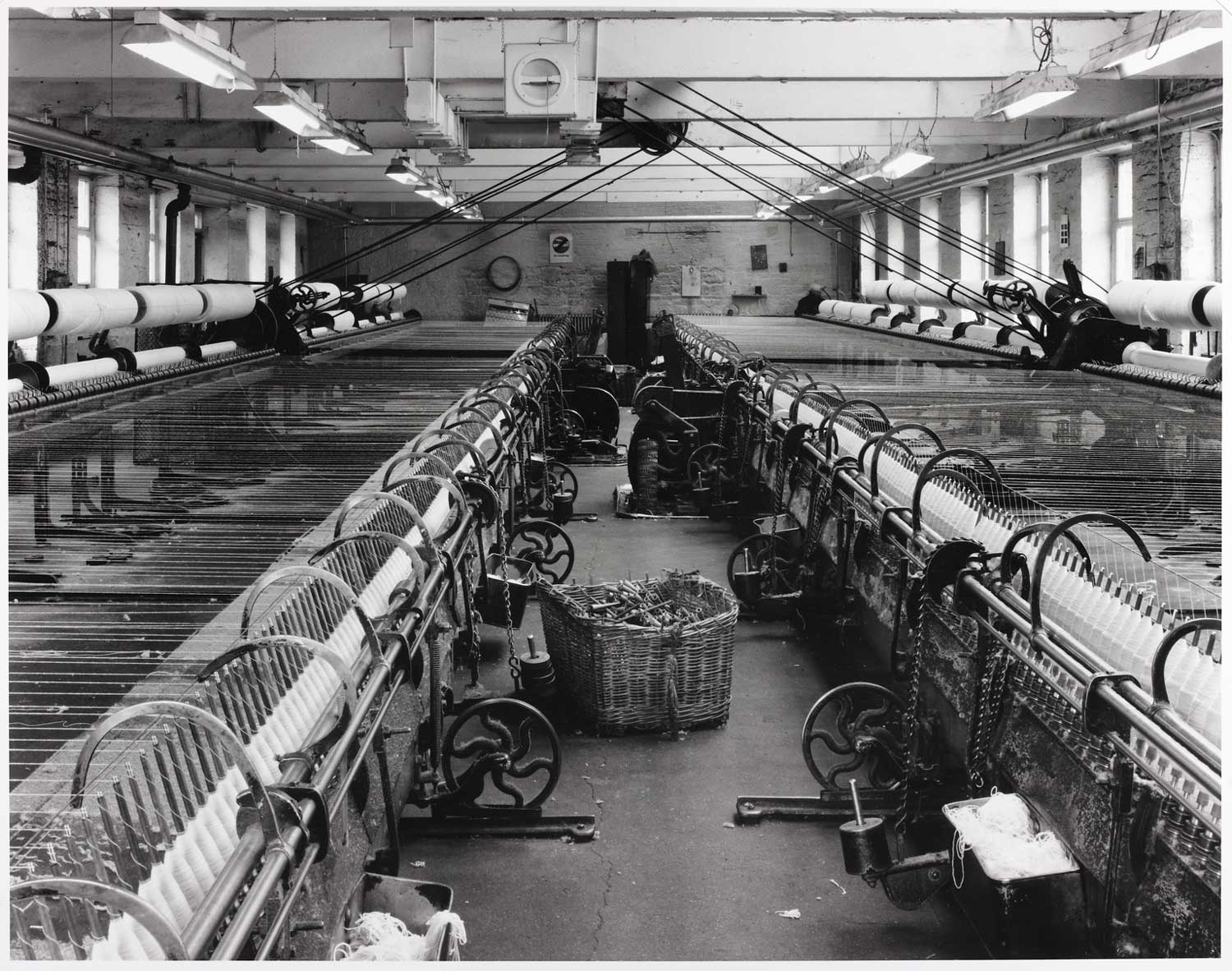
Credit: Ian Beesley/Science Museum Group Collection
Although waste was produced by every machine in varying amounts, the types of waste were very different. At one end of the scale was the soft, untwisted waste from the carding engine, which could be spun using a similar process to normal cotton, although it had shorter fibres and contained bits of leaf and twig. At the other end was the spinning waste, which had already been twisted so needed to be pulled apart before it could be respun. Special machines were used to process waste cotton to allow for the different characteristics and needs. Textile mill owners sometimes processed their cotton waste themselves but often they sold it to specialist cotton waste mills for spinning. The different types of waste were worth different amounts so they all had to be kept separate.
Waste cotton yarns were not as strong or elastic, meaning that they were usually only used for the weft in a woven fabric with a stronger, raw cotton yarn for the warp. However, they were softer and fluffier, which made them perfect for making warm blankets and absorbent dish cloths. Using some cotton waste in goods made them cheaper too. Cotton waste was used in all sorts of goods—from mopheads, to carpets and upholstery stuffing, to workmen’s overalls—making them cheaper to buy, while the mill owner made money from what would otherwise have gone in the bin.
Wool
From the early 1800s, worn out wool clothes were collected and torn apart until they were piles of reclaimed wool fibres or shoddy. This was achieved by putting them through a ragpicker or ‘devil’, so called because of the machine’s rows of metal teeth that ripped the fabric apart. This shoddy was often mixed with a small amount of new, ‘virgin’ wool and respun into yarn which could be made into cloth (also called shoddy) and eventually new garments. The shoddy industry was a way to make money from waste products but also dealt with increasing amounts of discarded cloth as the woollen industry boomed.
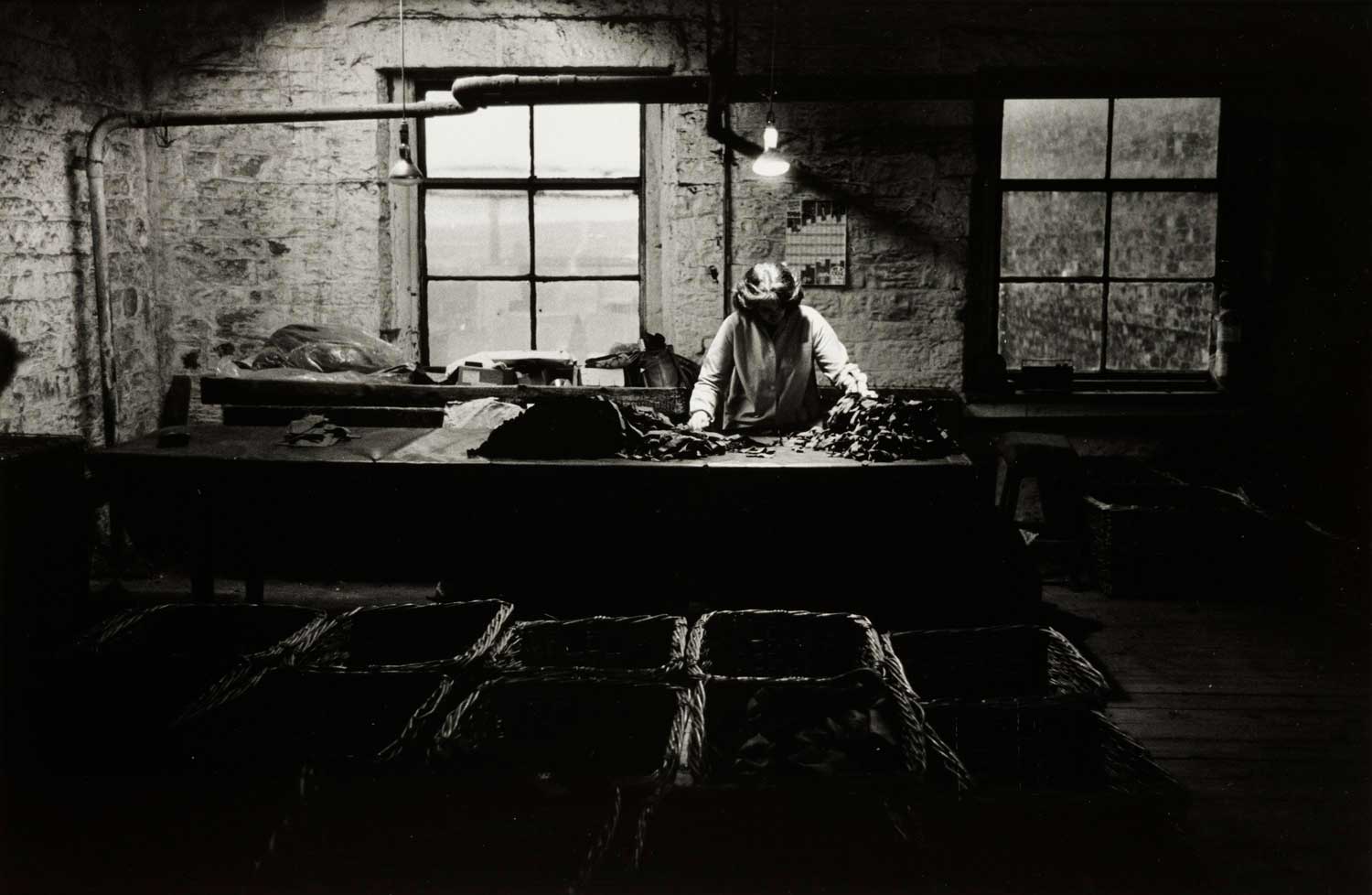
Credit: Ian Beesley/Science Museum Group Collection
One of the first uses for shoddy was blankets for enslaved people on American cotton plantations. Shoddy was cheaper than virgin wool so Benjamin Law, the apparent inventor of shoddy, saw a money-making opportunity to supply slave owners, who wanted to spend as little as possible on keeping their enslaved workers warm, with blankets at lower prices than they’d seen before. His first sales trip to the USA proved very successful, and on his return to his hometown of Batley in Yorkshire he shared the secrets of his success. A busy shoddy industry sprang up in the Yorkshire towns of Batley and Dewsbury, with many making handsome profits from selling shoddy or ‘slave cloth’, as it was sometimes known.
You may think of ‘shoddy’ as meaning something poor quality and a bit rubbish, but the shoddy industry came first and that meaning of the word actually comes from the recycled wool fabric. The mechanical shredding of rags damaged the wool fibres, making them frayed and bruised and less durable, so the fabric was less durable too. Shoddy was widely used for soldiers’ uniforms in the American Civil War because lots of material was needed in a short time and it was also cheaper than new wool. But the material was not robust enough for the hardships of war and the uniforms quickly began falling apart, leading to shoddy’s association with poor quality.
Papermaking
Old textiles have also been recycled into other products. For thousands of years, paper was made by pulping old cotton and linen rags and drying a thin layer of this pulp to make individual sheets of paper. The rags often came from old underwear; can you imagine reading a book made from old pants? The demand for paper meant that rags commanded a good price and their collection could supplement a household’s income and even become a job, such as a rag and bone man. The recycling of rags into paper continued to be important until the 1870s, when wood pulp began to replace rags in paper manufacture.
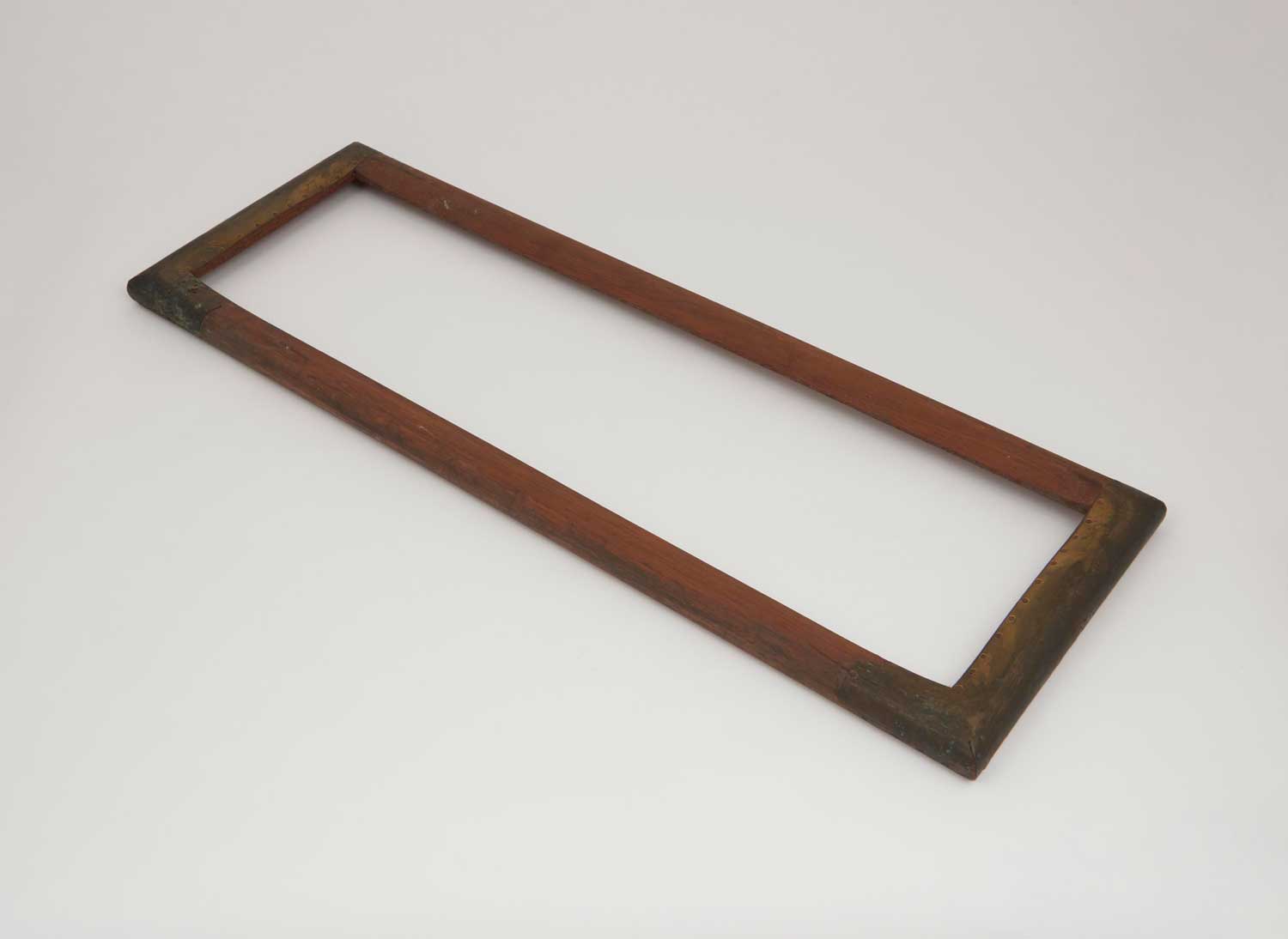
Credit: Science Museum Group Collection
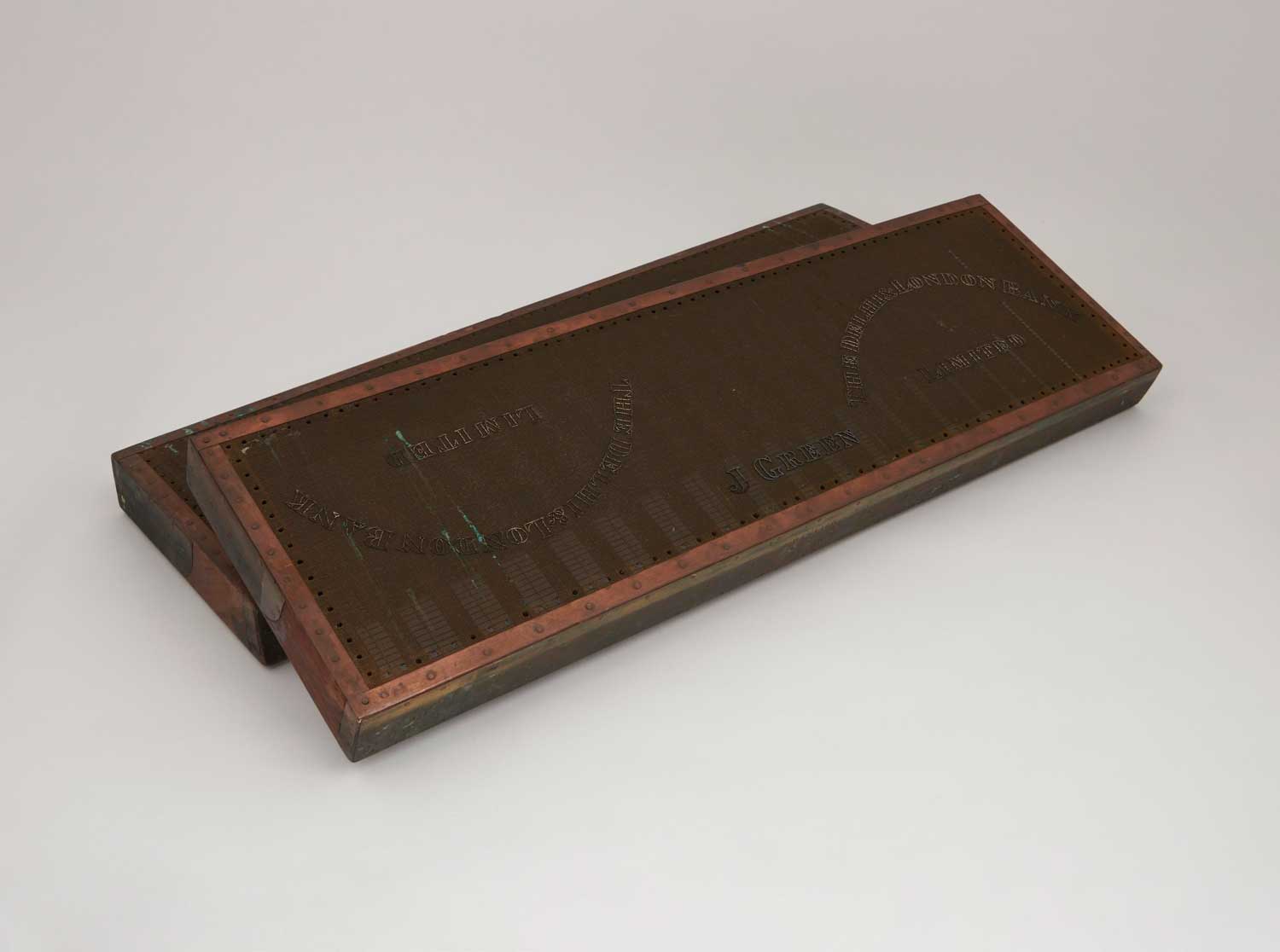
Credit: Science Museum Group Collection
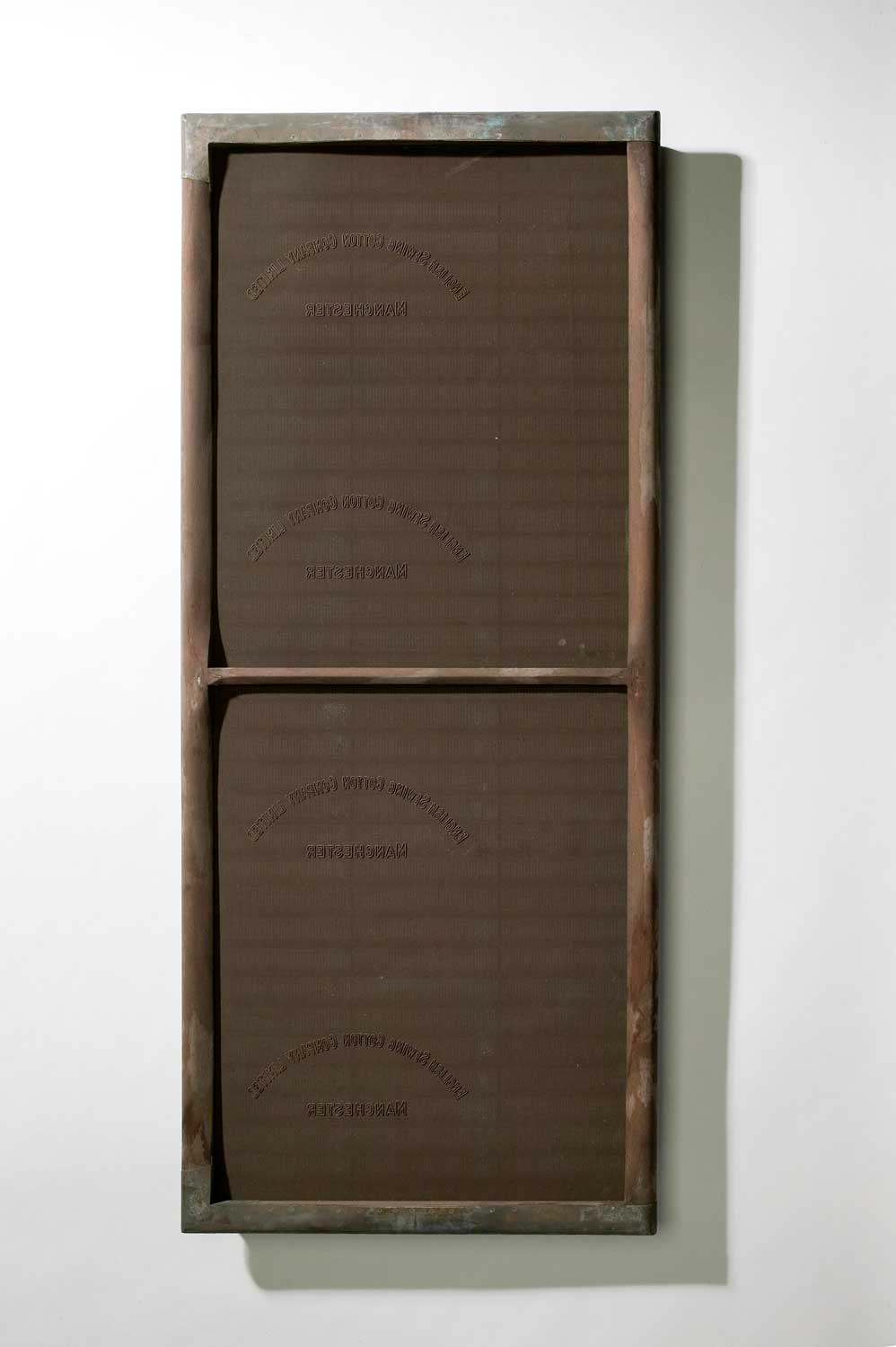
Credit: Science Museum Group Collection
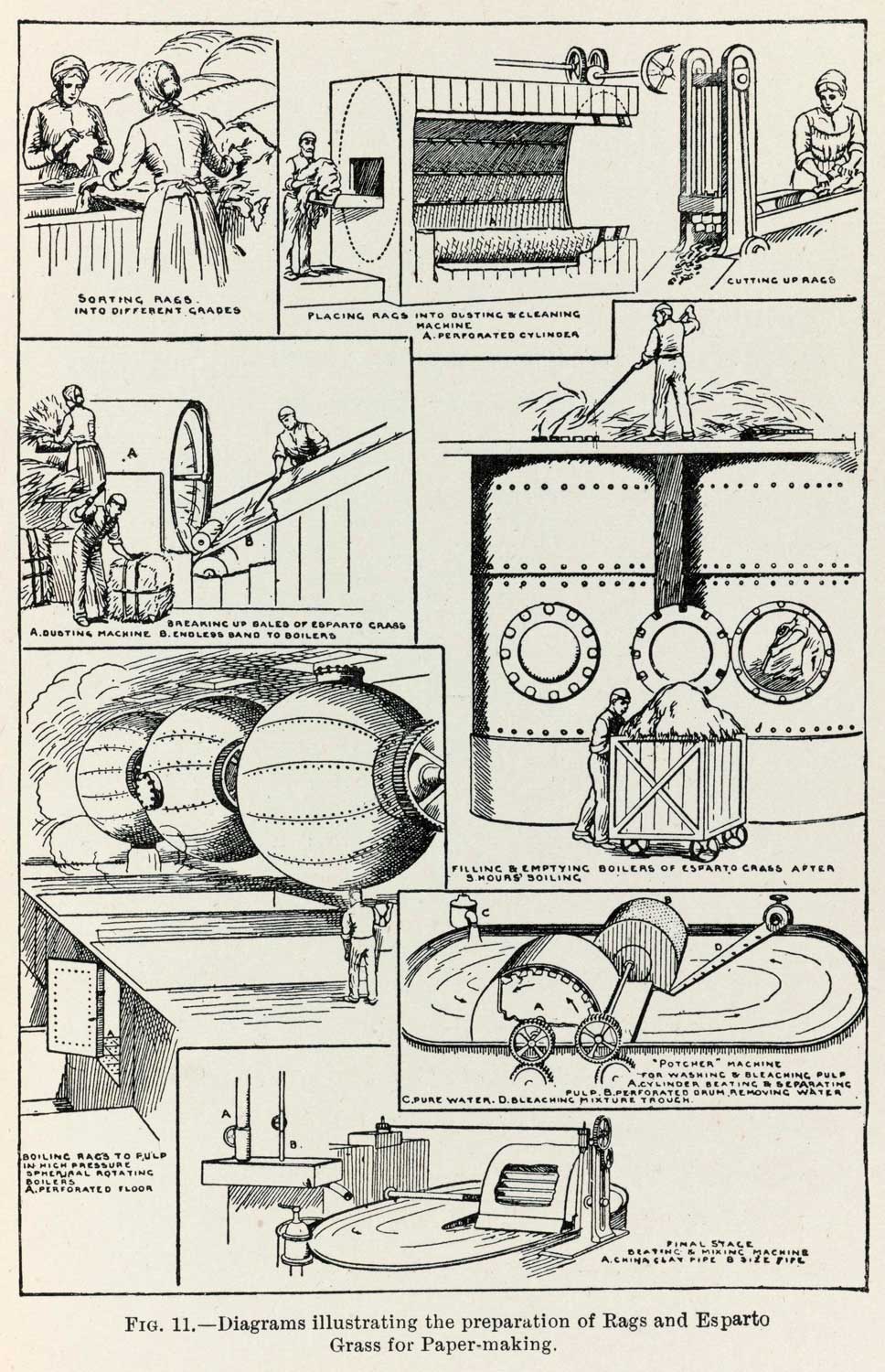
Credit: Science Museum Group Collection
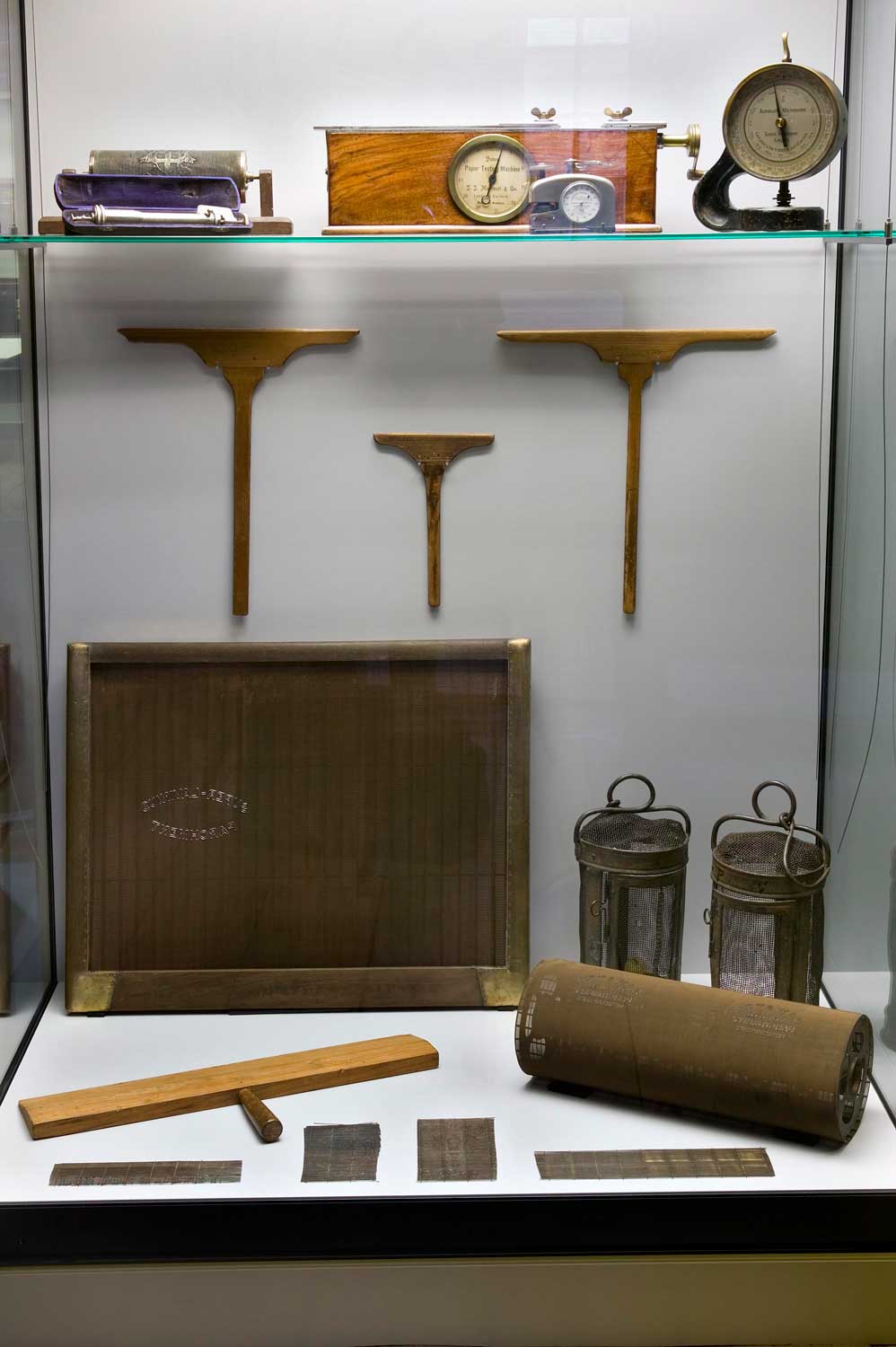
Credit: Science Museum Group Collection
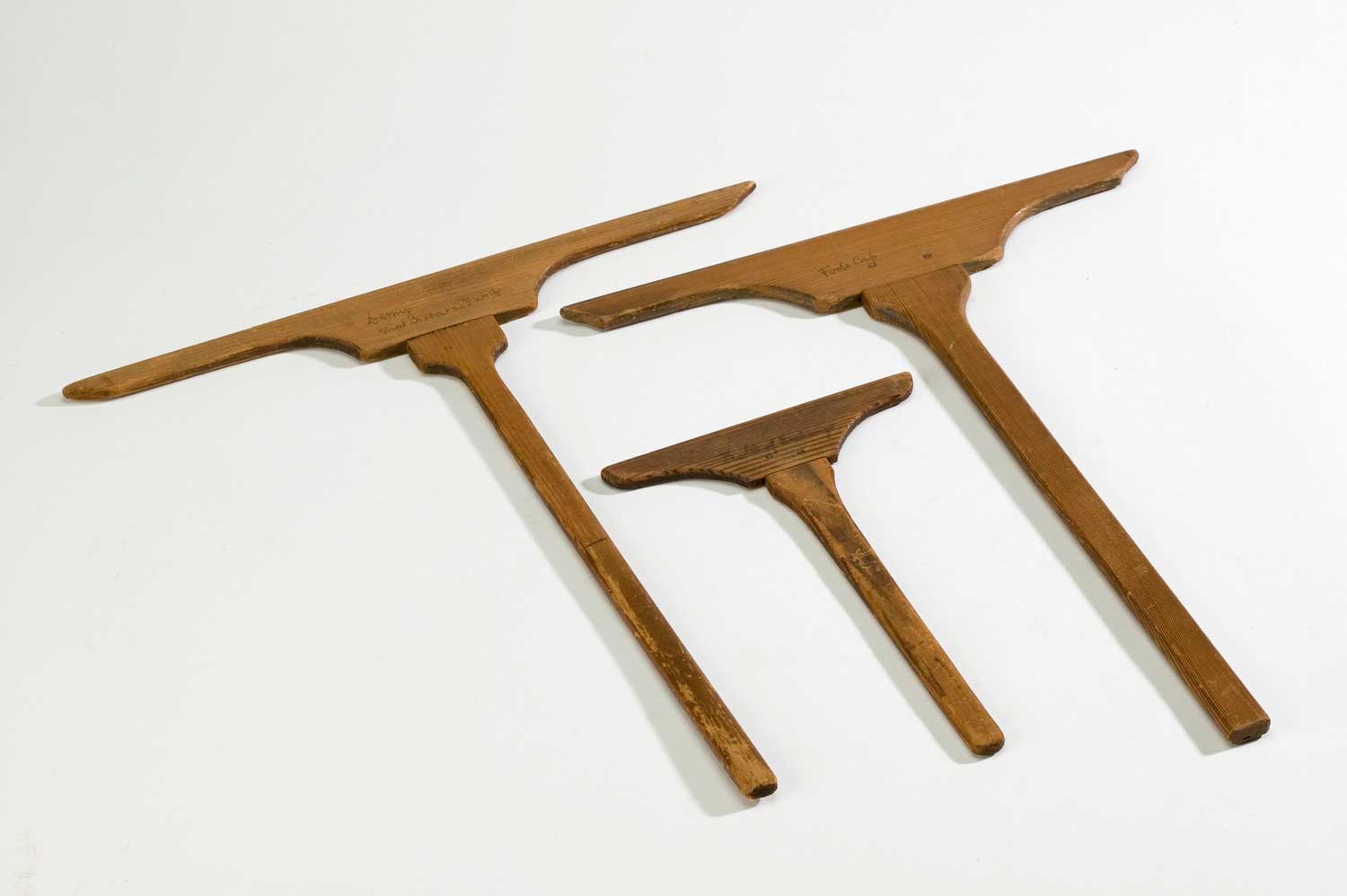
Credit: Science Museum Group Collection
So textile recycling and waste reduction is nothing new but the motivation in the past was usually money rather than caring for the environment. Many of the textile recycling techniques of today are remarkably similar to those used in the past but scientific advances are also making a big difference to the sustainability of our clothes and fabrics.
Find out more about sustainability in the textiles industry at the Science and Industry Museum in the Textiles Gallery, including our temporary exhibition in the Conversation Space. You can also read our accompanying post on modern sustainable textiles.