In this blog, Science and Industry Museum Collaborative Doctoral Partnership student Bethany Turner-Pemberton shares more about the graphene jacket and explores other objects from the museum’s textiles industry collection with extreme stories to tell.
Graphene-enhanced jacket
First isolated in Manchester in 2004, graphene is a one-atom thick, two-dimensional carbon crystal. It is the strongest, thinnest, lightest and most conductive material discovered. With its lightweight, strong and flexible properties, many clothing designers are experimenting with graphene to enhance textiles and apparel.
This jacket, made by London sportswear manufacturer Vollebak, is created from three layers of fabric, including an inner layer of graphene-enhanced fabric. This enables the jacket to store and redistribute heat, regulate the wearer’s body temperature, and reduce humidity next to the body. The jacket is also durable and extremely light. In addition to their graphene jacket, Vollebak also make a range of graphene-enhanced t-shirts, and the company say their mission is to ‘use science and technology to create clothes from the future’.
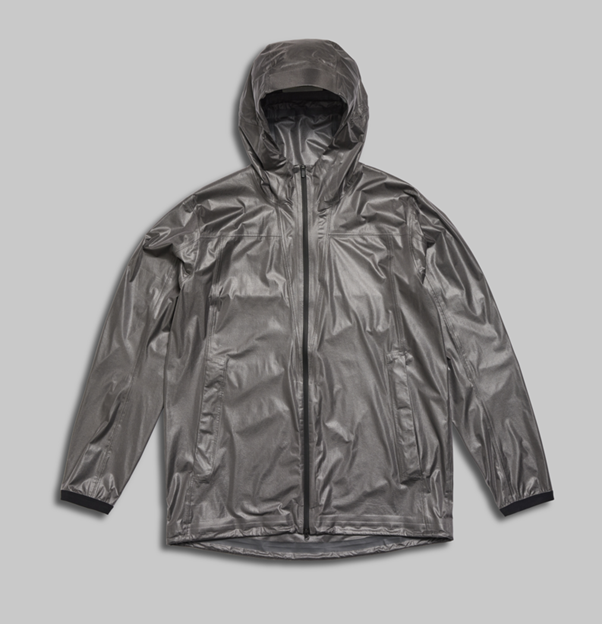
Image: Vollebak
More information
Graphene-enhanced trainers
These trainers, manufactured by Lake District-based sportswear makers inov-8, have a patented Graphene-Grip sole. This is designed to enhance the grip and durability of the shoes for rough terrain running and hiking. While they may look like other running shoes, the graphene-enhanced foam used in the sole is also far more resistant to compression, meaning the shoe maintains optimum levels of underfoot bounce and comfort over time. This technology helps rough terrain runners maintain a faster speed over longer distances and ensures that their feet feel fresher for longer. Like Vollebak’s graphene-enhanced jacket, the trainers were developed in collaboration with experts at the University of Manchester’s National Graphene Institute.
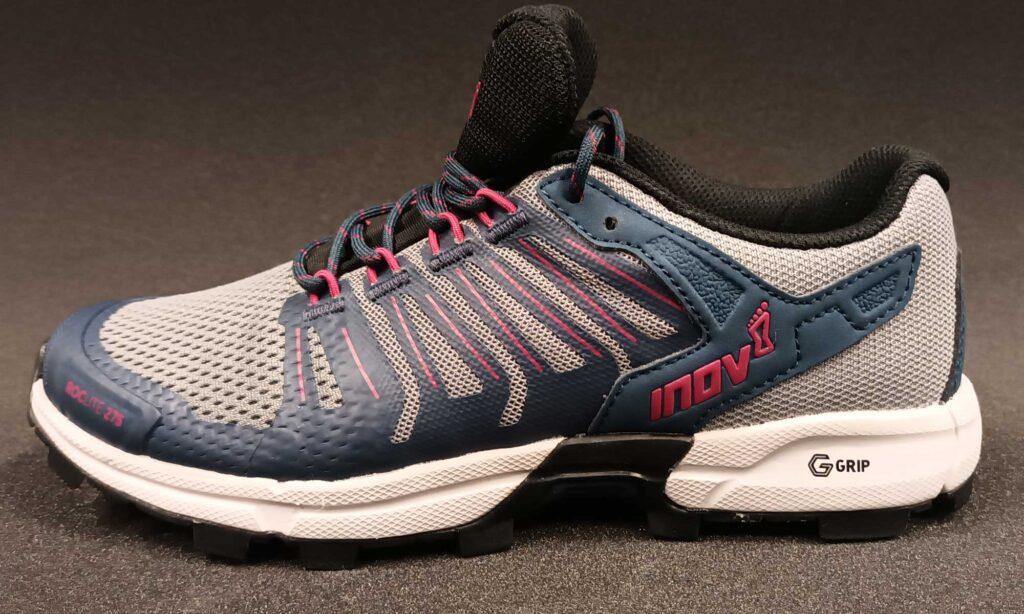
Science Museum Group © The Board of Trustees of the Science Museum
Immersion suit blouse
It isn’t only Manchester’s 21st century textile manufacturers who are developing textiles designed to push the boundaries of human performance. Founded in 1854, Manchester company P. Frankenstein and Sons Ltd specialised in making experimental, rubberised textile products from the Victoria Rubber Works in Newton Heath, and from the 1940s to the 1970s, they developed and produced innovative flight safety suits for pilots.
Their range included full pressure suits, which were designed to help pilots survive in extreme conditions when flying at high altitudes. In the event of decompression of the cabin, the suits could inflate and keep the pressure steady on the pilot’s body, helping them to breathe without blacking out.
The company also manufactured immersion suits, like the one on display in the museum’s Textiles Gallery, which were designed to protect pilots in case of a water landing. Rubberised textiles were the ideal fabric for these suits. Not only was the fabric flexible and comfortable, but the rubber coating acted as a barrier to the elements, keeping water out and heat in. P. Frankenstein and Sons’ technology eventually went on to inform the design of the Apollo spacesuits developed by NASA in the 1960s.
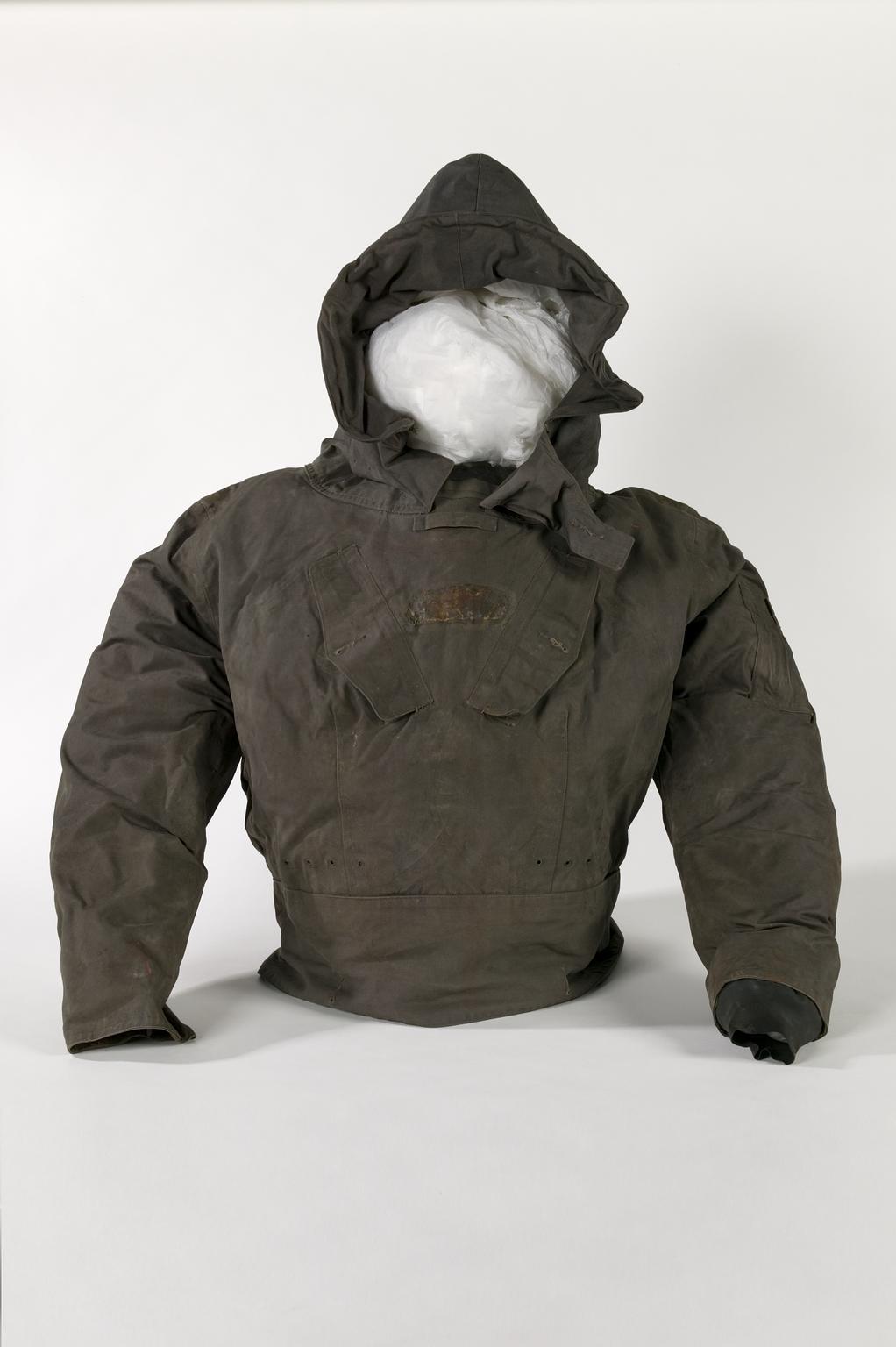
Science Museum Group Collection © The Board of Trustees of the Science Museum
More information
British Millerain waxed cotton fabric
In the 19th century, British sailors were using linseed oil to waterproof the sails of their boats. They used the same oil-coated fabric to make smocks to wear at sea and soon the Royal Navy started using linseed oil coatings for their uniform fabric. However, linseed oil cracks in cold weather and becomes yellow with age, meaning the fabric didn’t protect the sailors for long enough.
British Millerain was established in Rochdale in 1880 as a cotton finishing company to overcome issues with the linseed oil coatings. They developed paraffin-based wax to coat cotton fabrics instead. Paraffin waxed fabrics don’t crack or dry out and the wax can be reapplied regularly to maintain its waterproof properties. British Millerain became market leaders in waxed cottons, producing weatherproof fabrics for use in extreme conditions by the army and nvy, as well as in country pursuit and motorcycle clothing.
Today, British Millerain still produces waxed cotton fabrics on customised machinery using patented processes. The fabric samples in the museum’s collection are coated with traditional petroleum-based wax as well as innovative natural waxes, such as soy and beeswax. The fabrics can be recoated using tins of fresh wax, ensuring garments stay weatherproof and durable for longer.

Science Museum Group © The Board of Trustees of the Science Museum
Waterproof sailing suit
This waterproof sailing suit was made by Manchester company Henri Lloyd, which started life in 1963. In the early 1960s, man-made fibres were still in their infancy, but Henri Lloyd co-founder Henri Strzelecki realised the potential of a new technical fabric being produced by ICI called British Nylon. As a keen sailor, he was frustrated with the lack of available clothing able to withstand the marine environment. The company set up in a converted chapel and began manufacturing sailing wear, employing Nylon and other new man-made fibre technologies.
Amongst their innovations was the first non-corrosive zip, made out of Nylon, the first Velcro closure in waterproof clothing, and the first taped seams to ensure waterproofing, all of which feature on this sailing suit. Today, Henri Lloyd still has its headquarters in Manchester and the company continues to focus on innovation and new technology in sailing wear.
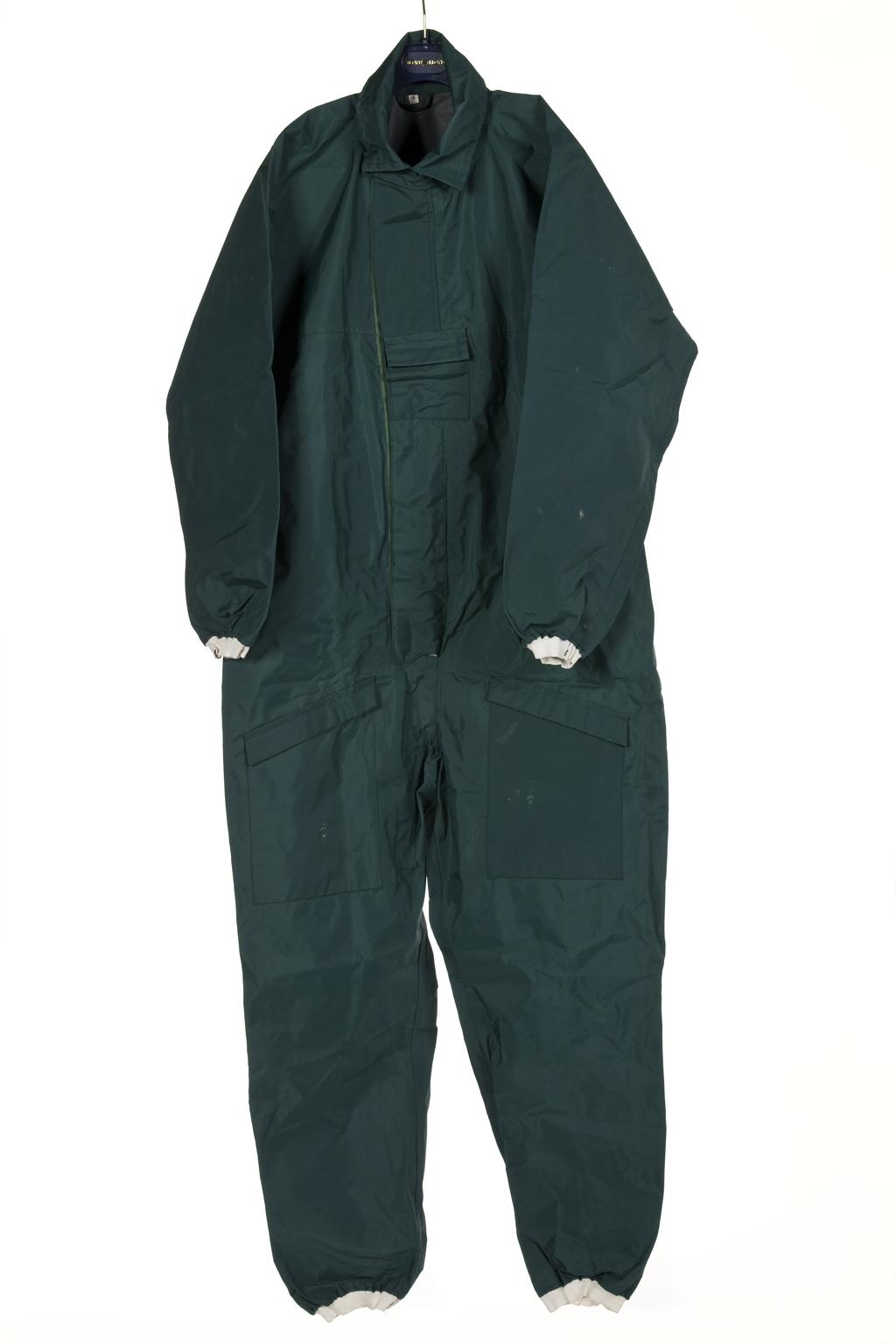
Science Museum Group Collection © The Board of Trustees of the Science Museum
More information
Virustatic SHIELD®
Another cleverly coated textile from more recent times, this Manchester-developed face covering offers extreme protection from airborne viruses. The Virustatic SHIELD® is made of fabric that is coated with a protein called Viruferrin®, which acts as a ‘germ trap’ to capture and disable viruses. This trapping technology prevents virus particles from spreading when people breathe in and out and reduces transmission from touching the mask and other surfaces.
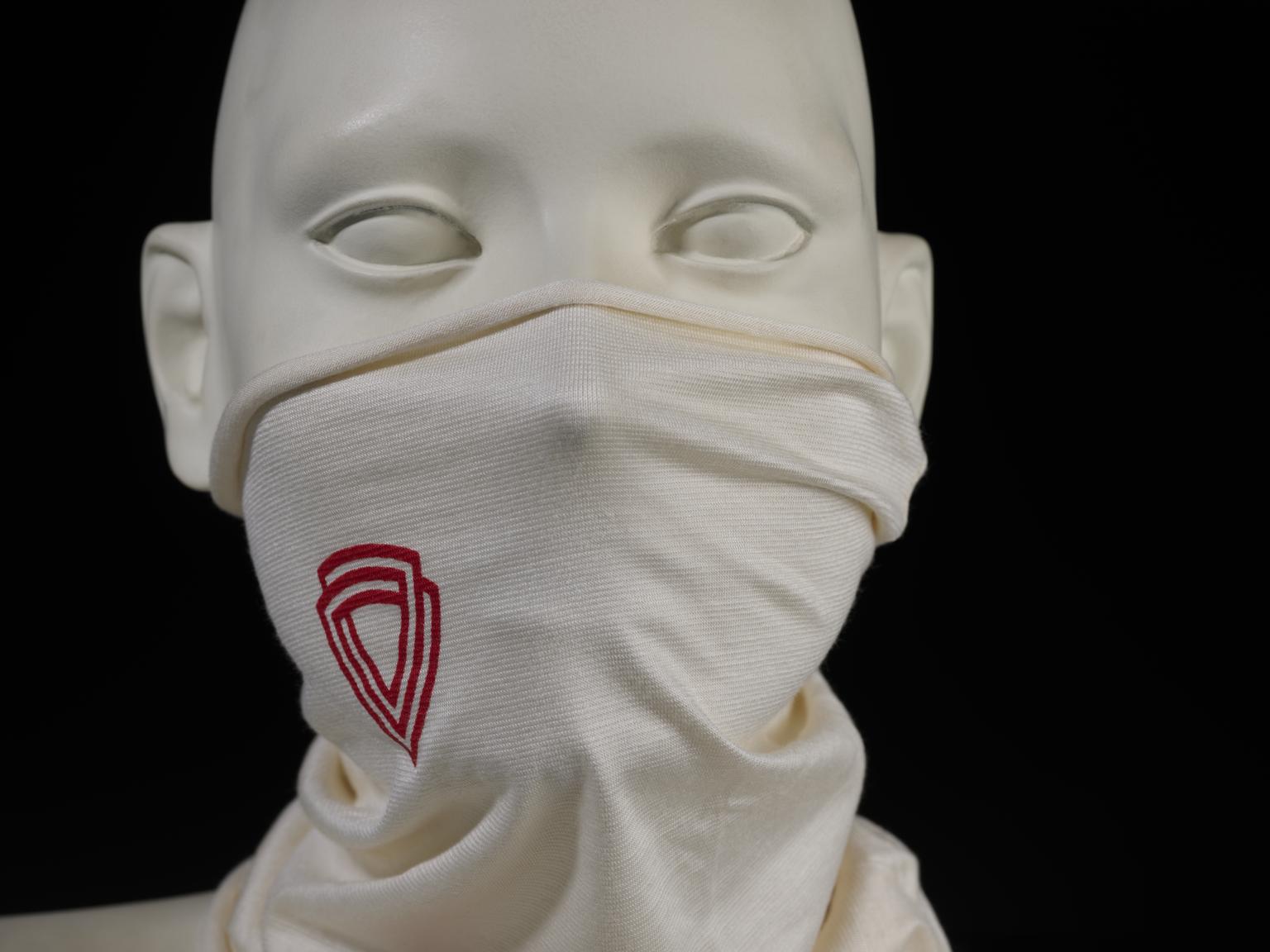
Science Museum Group Collection © The Board of Trustees of the Science Museum
More information
Unlike disposable face masks, the snood-style fit removes gaps around the cheeks and nose, stopping the entry or escape of virus particles. The SHIELD® is intended to be washed and reused and is knitted using a wood-pulp-based fibre, making this face covering a more sustainable option.
The Virustatic SHIELD® and the protein Viruferrin® are the result of research into pandemic preparedness by company founder Paul Hope in collaboration with the University of Manchester. The face covering came to market in March 2020, just as the global COVID-19 pandemic was taking hold, you can currently see one on display in Injecting Hope: The race for a COVID-19 vaccine.
English Fine Cottons
Based in a Victorian cotton spinning mill on the banks of the River Tame in Dukinfield, Greater Manchester, English Fine Cottons was established in 2016 and are the only cotton spinners manufacturing in the UK today. Born from a desire to reverse the decline in the British textile industry, English Fine Cottons drew on Dukinfield’s heritage as a centre of cotton spinning production from the late eighteenth to mid-20th century.
English Fine Cottons use semi-automatic machines operated by people to reinvigorate traditional methods of cotton spinning and produce cotton fabrics of extremely high quality. The cotton used to make the facemasks in the Science and Industry Museum’s collection is Supima Cotton from California, an extra-long staple cotton fibre, which produces smoother yarn when spun, ensuring softer, more durable fabrics when compared to shorter cotton fibres. English Fine Cottons can fully trace their cotton back to field and farmer, using innovative farming and manufacturing technologies to produce a more sustainable product.
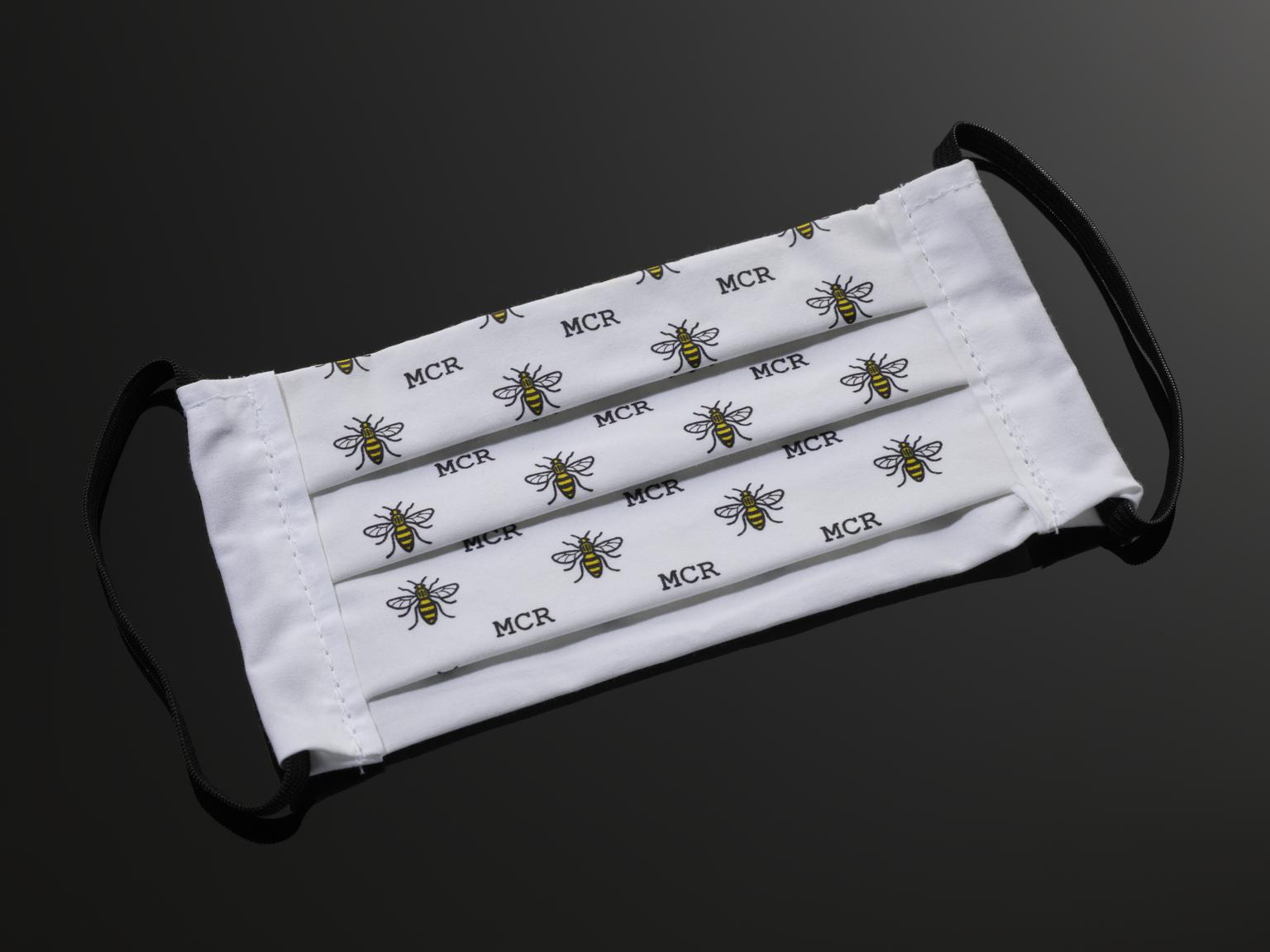
Science Museum Group Collection © The Board of Trustees of the Science Museum
More information
Martindale abrasion tester
Fabric manufacturing requires rigorous testing under extremely tough conditions. The Martindale Test is an internationally recognised measure of quality for textile fabrics. The test is carried out using a Martindale abrasion tester like this 1976 model from the museum’s collection. The test uses circular, looping patterns to rub and stretch the cloth in all directions. Samples of fabric are stretched over the round drums on the top of the machine and are then rubbed by the arms of the machine. Abrasion readings are taken to determine how quickly the fabric becomes worn and develops pilling; the longer it takes for bobbles to appear on the fabric, the stronger and more high quality the clothing.
This machine was used by The Shirley Institute in Manchester and by British Textile Technology Group in Trafford until 2018. Martindale abrasion testers like this model are still in use across the textile industry today.
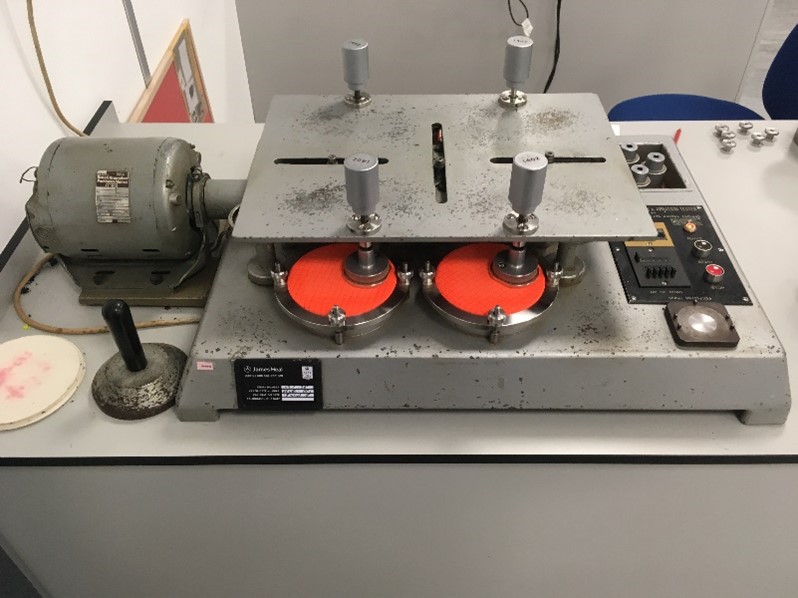
Science Museum Group © The Board of Trustees of the Science Museum
More information
These textiles stories are part of Bethany Turner-Pemberton’s PhD research. She has been working with the museum’s textiles industry collections and has conducted interviews across Greater Manchester’s textile industry to readdress the perception of decline in the region’s textile industry today.
Bethany’s research highlights new textile stories that deepen our understanding of how Greater Manchester’s textile industry operates today. Her work challenges long-established assumptions about the city’s textile heritage. As a result of her research, contemporary textile objects showcasing innovative textile research and production in Greater Manchester have been added to the museum’s object handling collection. The textiles stories Bethany has identified are enabling the museum to further understand the contemporary textile industry today and demonstrate the collaborative work of industries such as textiles, science and technology. Bethany’s research will be used to inform future exhibition development at the museum and to develop the way the museum tells these stories in the future.